1 Project background
In the context of intensified Sino-US trade war frictions, the competition for autonomous control of semiconductor materials has intensified. Especially in recent years, my country’s new production capacity has become the main increase in global fabs, but the upstream key raw materials and production equipment that restrict the strengthening of the semiconductor industry are still almost monopolized by American and Japanese companies. It is the further blockade of the chip industry, which is almost a blow to the development of my country's semiconductor industry. Therefore, the strategic position of the localization of semiconductor materials has been highlighted, and the acceleration of the import substitution process in the material field is a general trend.
2 Product description
CMP (ChemicalMechanicalPolishing) chemical mechanical polishing is a combination of chemical corrosion and mechanical friction. It is currently the most common semiconductor material surface smoothing technology. It combines the advantages of mechanical friction and chemical corrosion, thereby avoiding surface damage caused by simple mechanical polishing and slow polishing speed, surface flatness and polishing caused by simple chemical polishing. Disadvantages such as poor consistency. A relatively perfect wafer surface can be obtained.
It is generally accepted internationally that when the feature size of the device is below 0.35μm, global planarization must be performed to ensure the accuracy and resolution of lithographic image transmission, and CMP is currently almost the only technology that can provide global planarization. The principle diagram of its equipment is as follows:
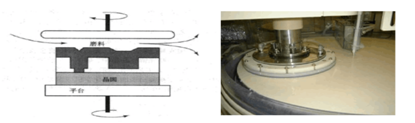
Grinding fluid: liquid substance added during grinding. The particle size is related to defects such as scratches after grinding. The larger the particle, the greater the damage to the wafer, and the smaller the particle, the better. The basic form is composed of nano-powder polishing agent and an alkaline component aqueous solution. The particle size is 1-
100nm, the concentration is 1.5%-50%, the basic composition is generally KOH, ammonia or organic amine, and the pH is 9.5-11.
Due to the high purity of the fumed silica, the controllable original nanometer particle size and particle size distribution, the fumed SiO2 becomes the main abrasive in the oxide polishing slurry.
3 Project materials:
Metal silicon powder, hydrochloric acid, hydrogen. Annual production of 1,000 tons of nano gas phase titanium dioxide project Annual production of 20,000 tons of special paper special light calcium carbonate project Annual production of 1,000 tons of BIPB (odorless DCP) project Continued research and development
4. Project supporting facilities:
Chemical industrial parks, steam, electricity, industrial water.
5. Technical advantages
Patent: A device for producing silicon dioxide and metal oxide by gas phase method
Patent: A device and process for producing high-purity trichlorosilane and silicon tetrachloride
6. The total investment of the project is 150 million yuan.
7. Project area: 30 acres
8. Economic benefits
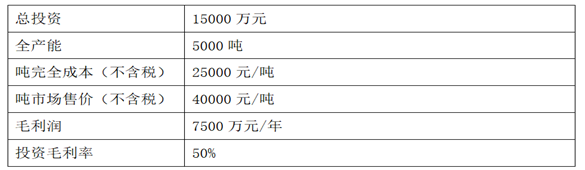